業務内容
- HOME
- 業務内容
- 素材・在庫販売部門
素材・在庫販売部門
主力はSUS304。日本最大級のストック量を誇ります。
弊社の主力鋼種は、ダム、水門、大型チャンバーに最適なSUS304です。総ストック量9,000トンを常時保持しております。その中身も①板厚1.0mm~100mm、②最大幅、最大長さ3,200mm ~8,100mm、③表面肌No.1に、両面80番研磨品と、ステンレスソリューションカンパニーとして業界トップクラスを誇る弊社の対応でお客様の幅広いニーズにお応えいたします。
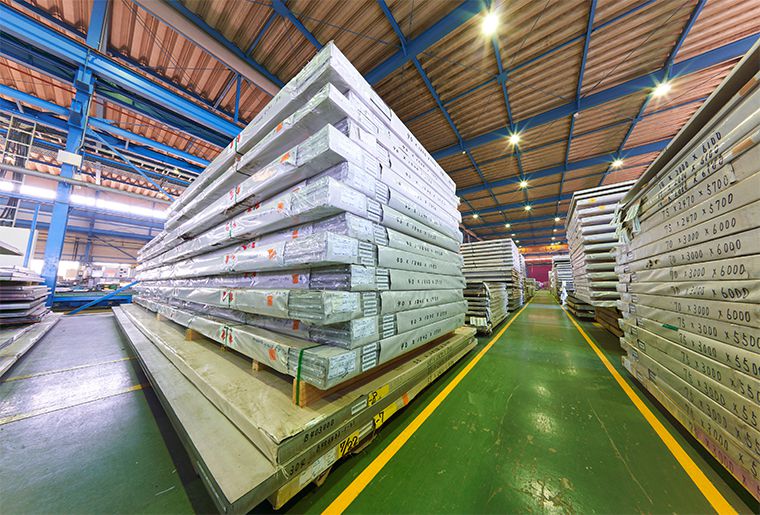
素材ヤード
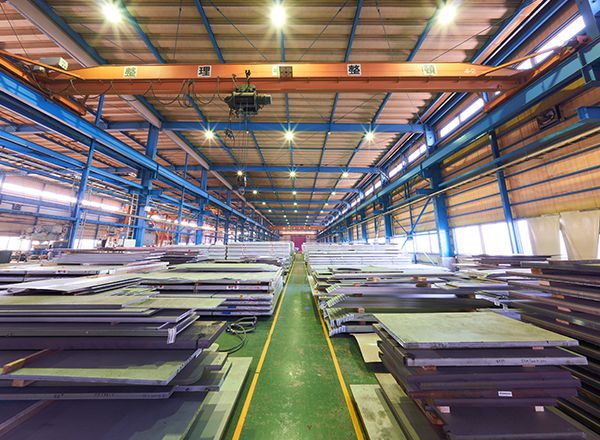
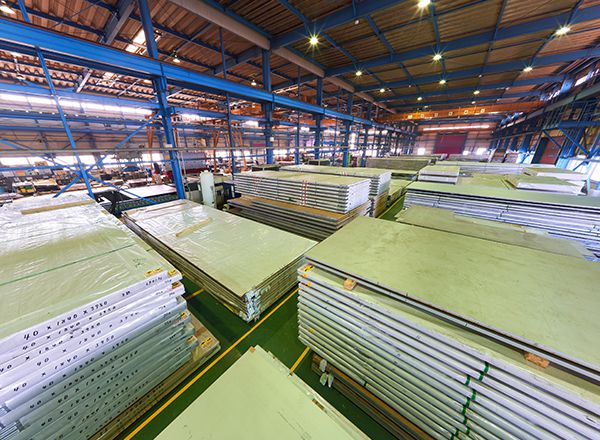
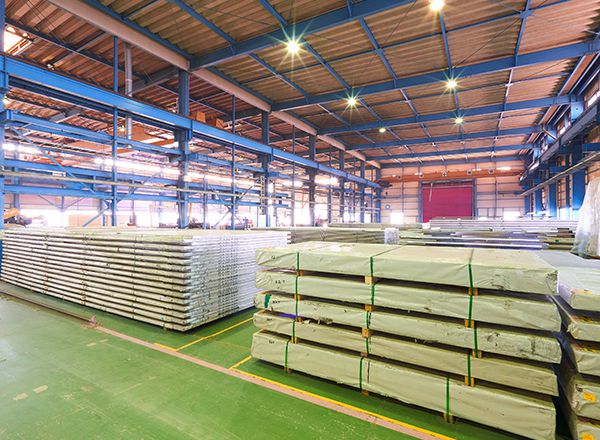
加工・製造部門
社内一貫生産で、品質の高い製品をご提供いたします。
切断、製缶・溶接、機械加工、電解研磨、板金等のステンレス加工を行います。現在は、真空チャンバーの製造及び半導体製造装置等の一部機器を製造しています。その他試作品から量産まででもステンレス製品の製造まで対応致します。
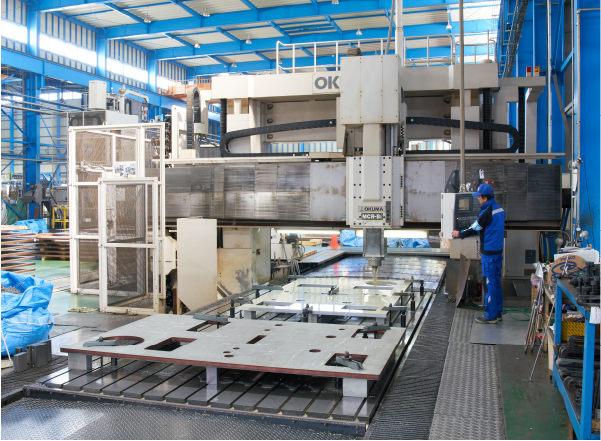
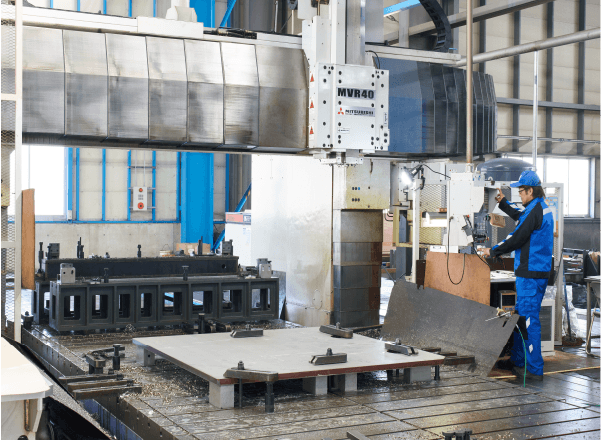
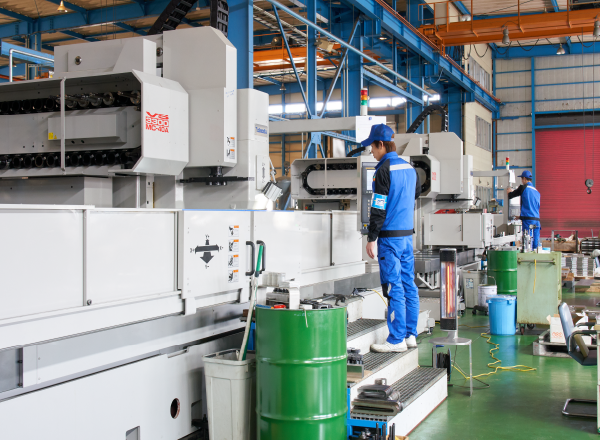
素材切断部門
正確で滑らかな切断面質は、これからのスタンダードになります。板厚25mmまで切断可能な「レーザー切断」をはじめ、最大板厚100mmを切断する国内屈指といわれる「ドライプラズマ切断」、さらには熱応力を極限まで減らした「水プラズマ切断」など、ニーズに応じた素材切断が可能です。最大切断幅は、4,500mmです。
熟練の技術者によるクオリティを重視した切断作業は、正確で断面の仕上がりも美しく滑らかと大変喜ばれております。お客様のご要望に合わせて複雑な形状にも対応しておりますので、お気軽にご相談ください。
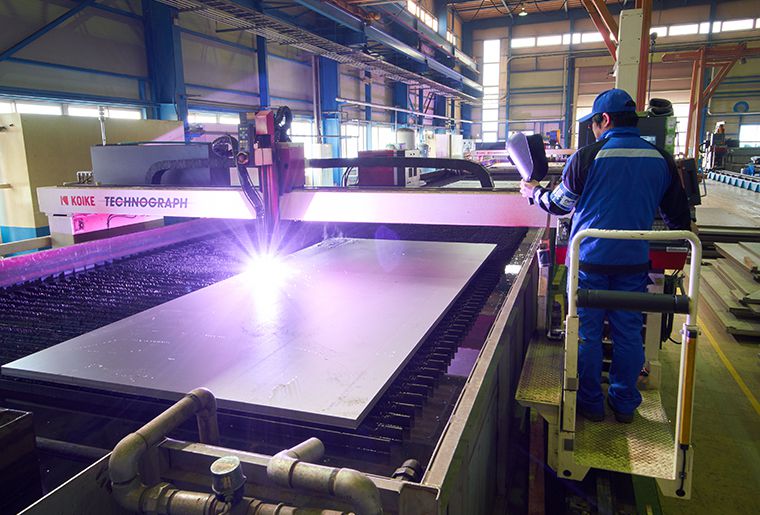
ドライ/水 プラズマ切断機
切断の種類
切断方法は3種類あります。
レーザー切断は複雑な形にも対応します。多少コストはかかりますが、その分精密で綺麗な断面に仕上がります。
ドライプラズマ切断、水プラズマ切断はレーザー切断に比べ少々切断面が荒くなりますが、コストを抑えて切断作業を効率的に行うことが出来ます。
お客様のご要望に合わせて切断致しますのでお気軽にご相談下さい。
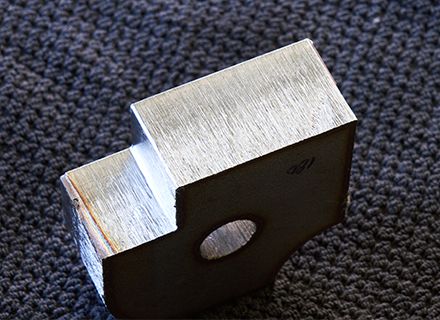
- レーザー切断
- 板厚25mmまで
高精度の切断が可能で複雑な形にも対応できます。精密できれいな断面に仕上がります。
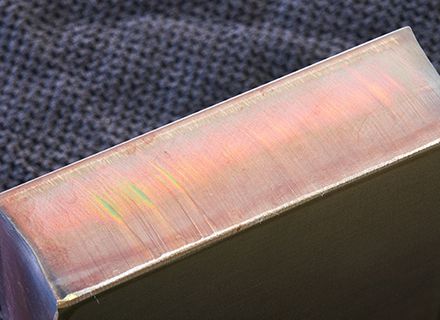
- ドライプラズマ切断
- 板厚100mmまで
厚さのある素材を切断します。切断面は国内屈指。
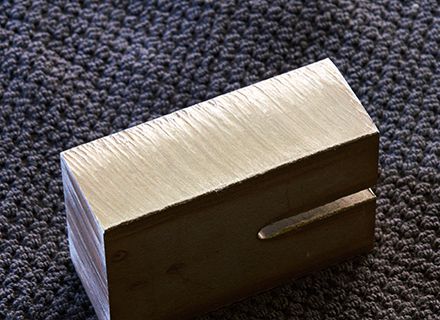
- 水プラズマ切断
- 板厚40mmまで
水中で切断することで熱応力を極限まで減らしました。騒音や粉塵など環境にも配慮。コストを抑えて作業を効率的に行います。
矯正・板金・研磨作業部門
「重・厚・大」のステンレス素材をお客様のご要望に合わせて加工いたします。
希望の寸法に切断した素材を矯正機にかけてフラットな状態にした後、板金、研磨加工の作業を施します。研磨では熟練した作業者が残粉の徹底除去を心掛けております。
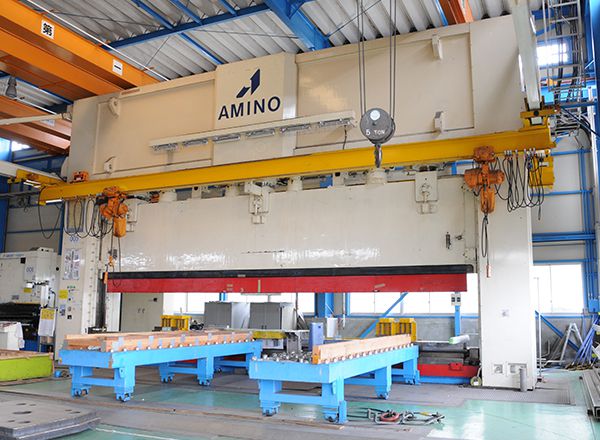
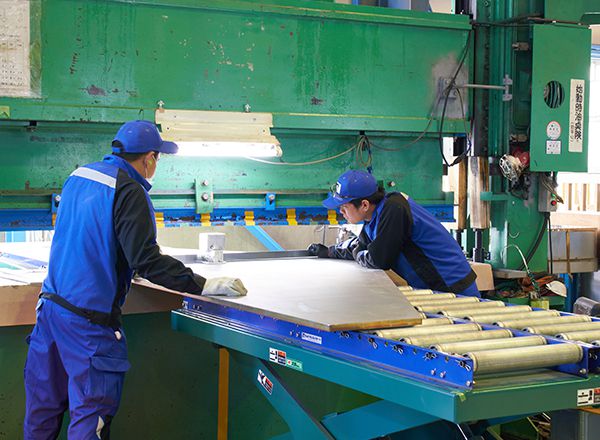
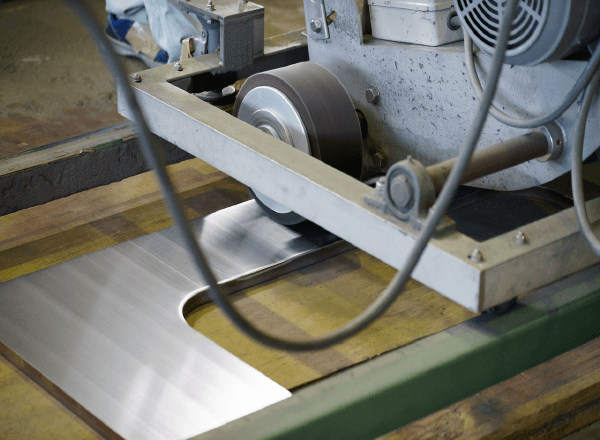
第一次機械加工部門
立体になる一歩手前の加工作業。熟練の技が光ります。
第一次機械加工は、矯正、板金、研磨を経た各部材を平面から立体にしていく前段の作業です。①溶接前の開先加工、②溶接前の側面切削、角穴、丸穴加工、③タップ穴、ネジ穴、溝加工などを行います。
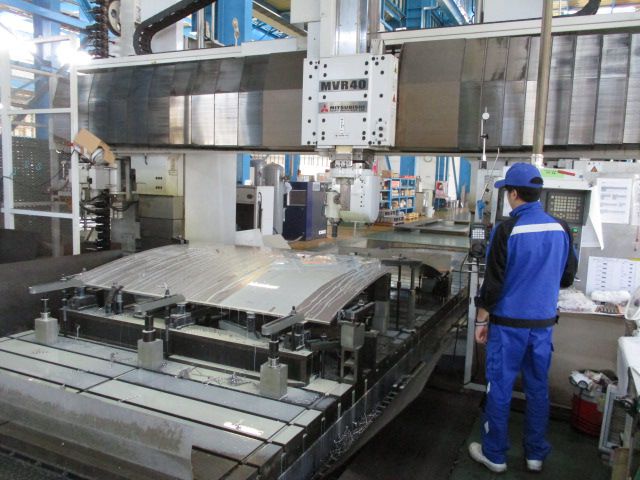
製缶・溶接部門
平面から立体へ。群を抜く技術力でニースに応えます。
ステンレス溶接は、変形(ひずみ)が大きく知識と経験を積んだ職人の技が必須です。長年にわたり積み重ねてきた弊社のステンレス溶接(Tig溶接)の技術力は、お客様から高い信頼を得ています。特に大型チャンバー溶接技術は業界でも群を抜いています。
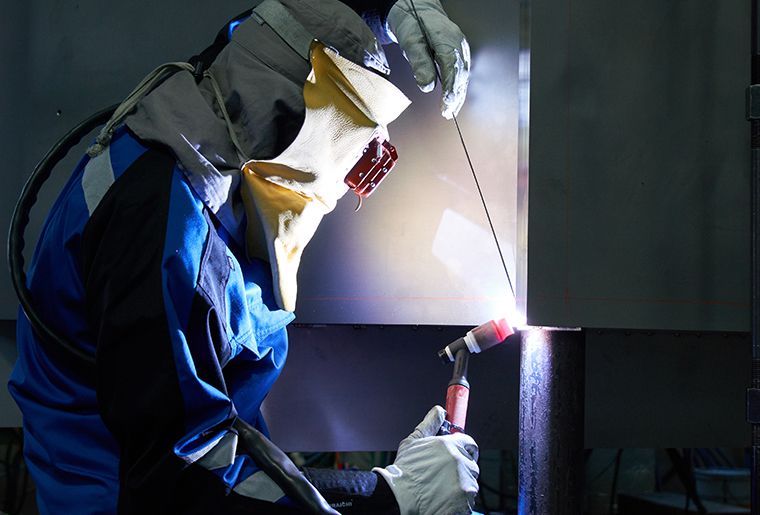
第二次機械加工部門
国内有数の規模で小型から大型までのワークサイズに対応しています。
第二次加工で精密な機械加工を施します。弊社では、大型縦型マシニング機械群を13台保有。さらに大型横型マシニング機械群を8台保有し、小型から大型までのワークサイズに対応いたします。その規模は、国内有数を誇ります。
さらに山元臨海第一工場においては社内初の恒温室加工が可能になりました。
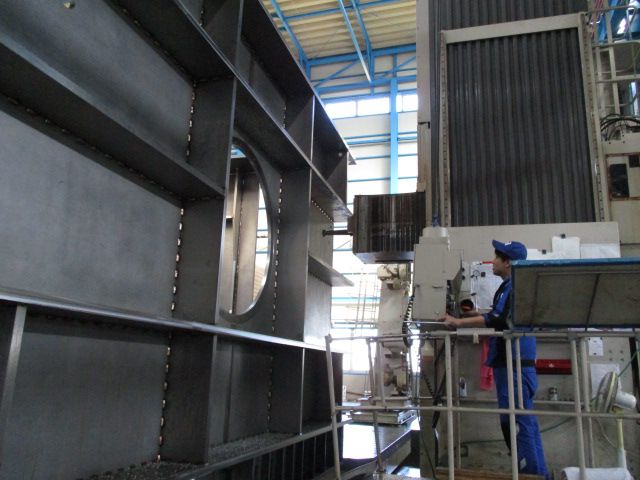
電解研磨部門
質の高い電解研磨でIT技術を支えています。
電解研磨によってステンレスの表面にある不純物・油脂を抑制し、強固な不動体皮膜を形成します。現代のIT技術は、電解研磨から生まれる鏡のような「表面」に支えられています。弊社では、大型電解槽1号機と2号機があり、最大で長さ8,000㎜×幅4,500㎜×深さ4,500㎜の大型槽です。製品洗浄には欠くことのできない純水製造プラント(日本オルガノ製)のほか、環境マネジメントシステムISO14001の基準に合致した排水処理部門も設置しております。
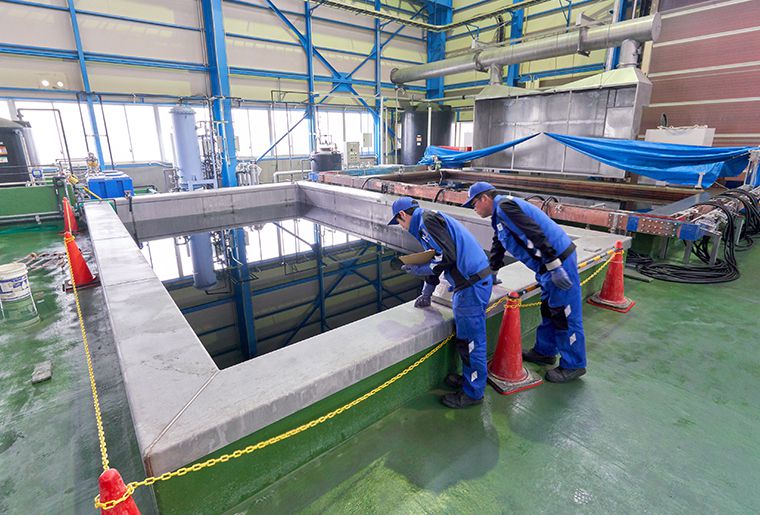
精密洗浄部門
精密洗浄ができる優れた環境があります。
液晶パネルや半導体チップの製造工程に使われる真空容器など関連装置の高精度化に伴い、これら装置部品の不純物を確実に除去する精密洗浄が求められています。理由は、微量でも製作時の不純物が残っていると成膜時に重大な支障をきたすことになるからです。
弊社では、常に徹底した精密洗浄を施してお客様に納品しています。
国内初!大型チャンバー精密洗浄プロセス
純水を90℃の高温にしてチャンバーを1時間から2時間、洗浄槽内に浸漬け投入し、チャンバーの温度が90℃に行き渡ったところで引き上げ、瞬時に起きる蒸発作用で急速乾燥。ネジ山、溶接の穴から酸を除去し、表面を撹拌し精密洗浄します。
精密洗浄を大型製品に適用するこの洗浄方式は、お客様の声に応え弊社が技術開発したもので国内初です。
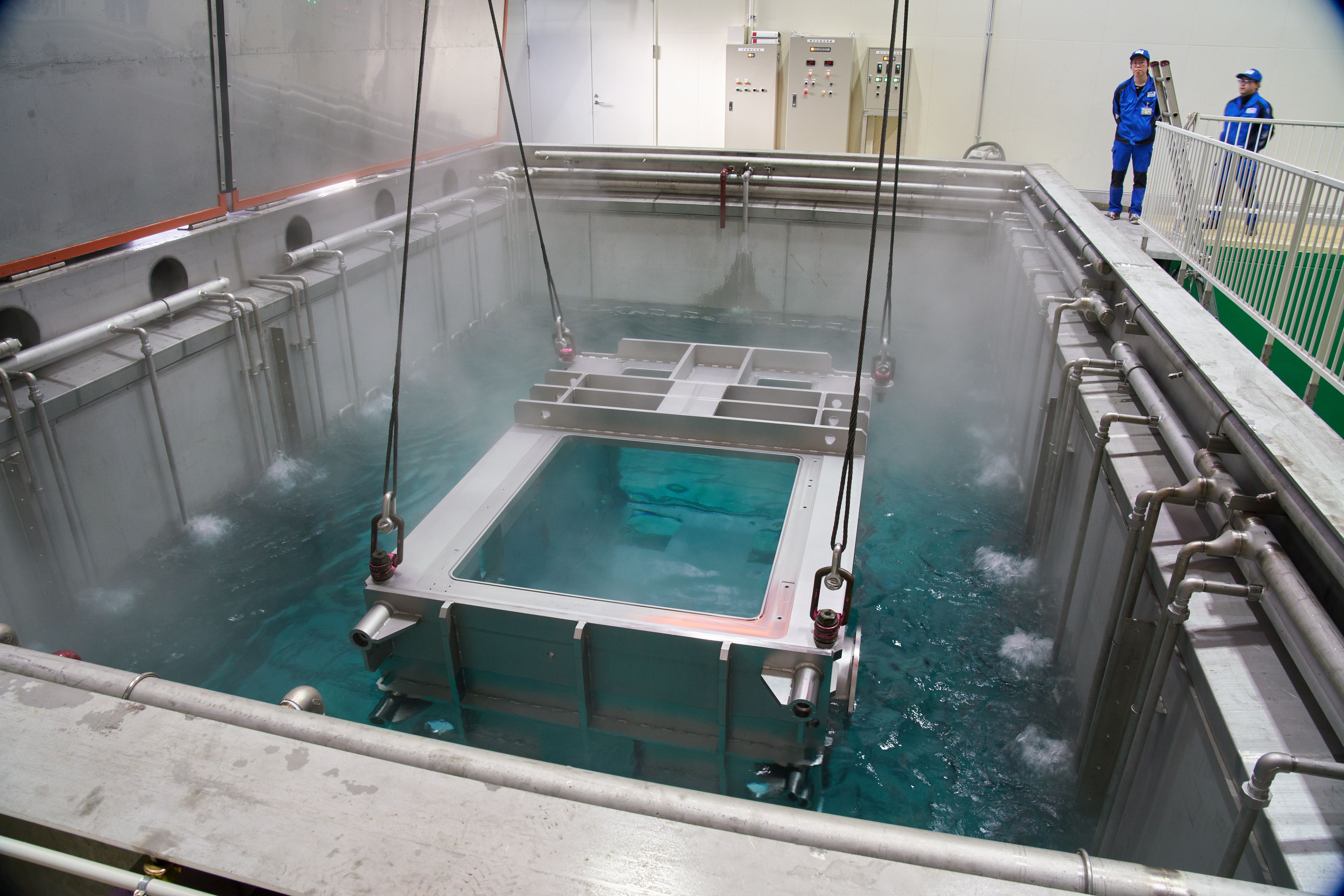
精密洗浄槽
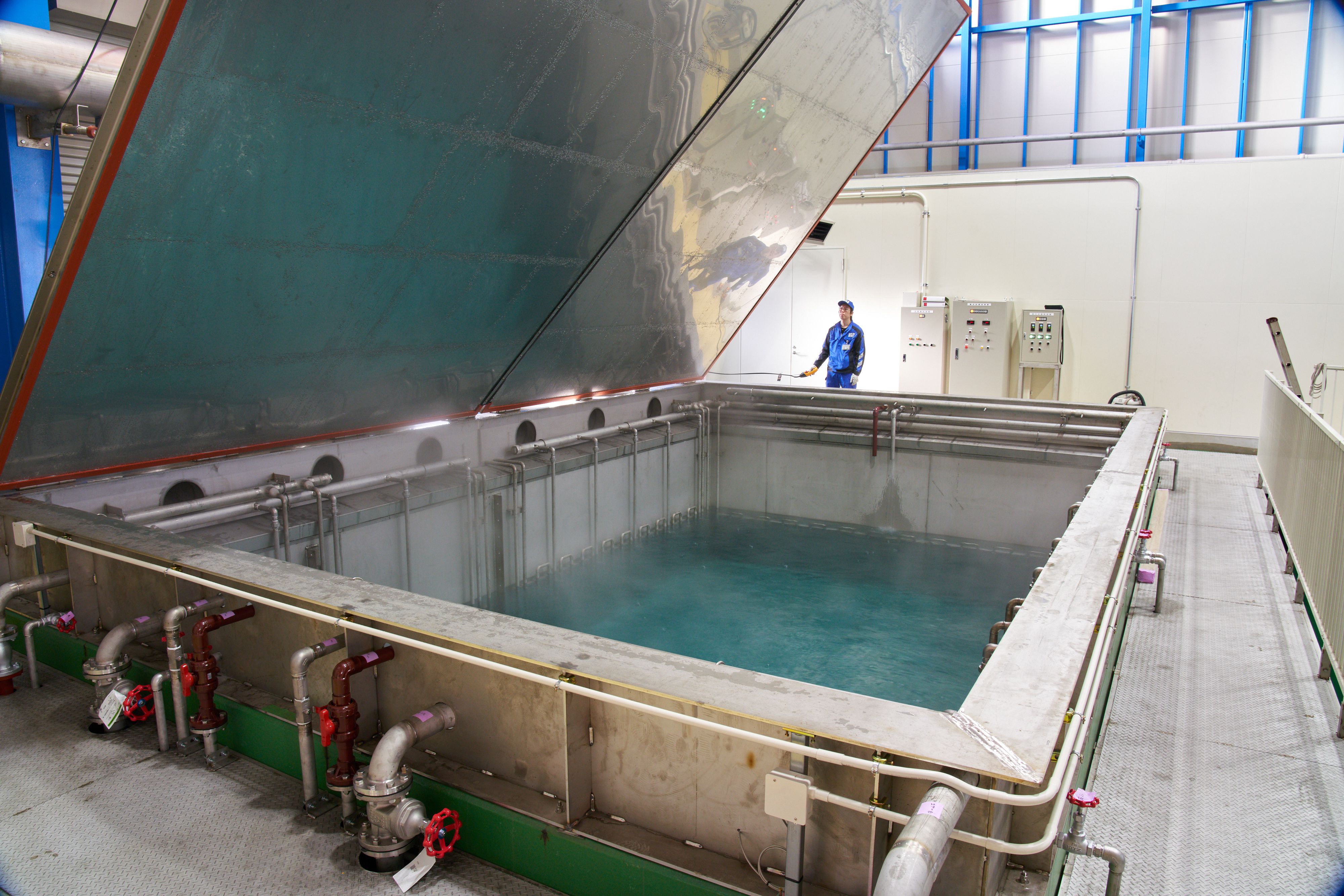
リークテスト・精密仕上げ・梱包部門
信頼の源。真空を保証するリークテスト
真空中で金属などを加熱・蒸発させ、蒸気をほかの物質の表面に薄い膜として付着させること蒸着といいます。真空中でないと付着できないことから、真空チャンバーのリークテスト品質検査は必須です。弊社では、厳しい目で漏れを検査、品質を保証して出荷しております。確かなリークテストが、メルコジャパンの信頼の源となっています。
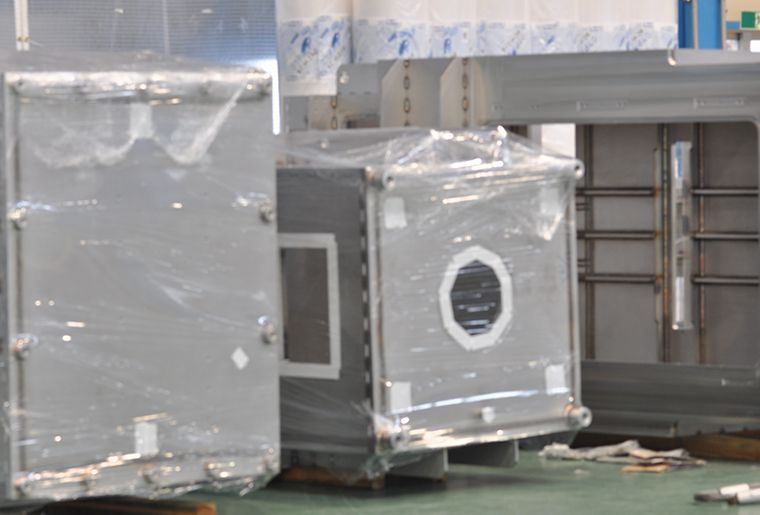
平成27年 山元臨海第一工場(一工場・二工場・三工場)稼働!
国の被災地向けの補助金を活用したメルコジャパンの最新工場です。雇用創出で地域に寄与します。
一工場は、端材小物精密溶断や自動運転切断、ファイバー・CO2レーザー切断など切断を専門に担います。二工場は、精密機械加工、半導体部品加工、さらに国内外で需要が伸びている航空機部品加工を行います。三工場は精密洗浄からリークテスト仕上げ、組立、梱包、出荷までを担います。
宮城県山元臨海第二工場新築予定です
山元臨海第一工場隣に半導体工場を新築予定です。工場は連続加工工場、精密洗浄工場でより省力化で高品質な技術を目指します。
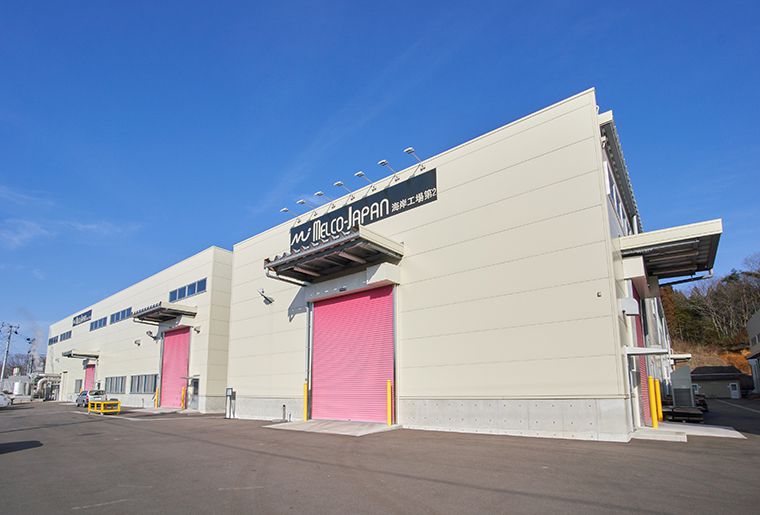